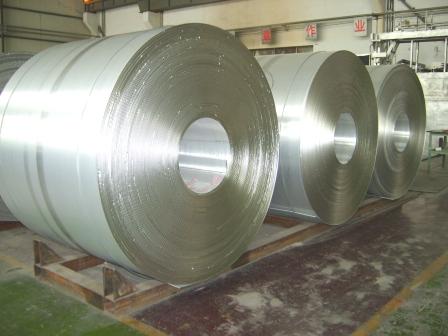
A metal casting and rolling method in which liquid aluminum is continuously made into blanks through rotating crystallizer and rolled into plates and strips at the same time (see continuous casting and rolling). The industrial test of light alloy continuous casting was carried out in the 1930s. In 1955, an aluminum strip continuous casting mill was made in the United States. Later, many other types of continuous casting mills appeared. Compared with the traditional ingot hot rolling and cold rolling method, the main advantages of continuous casting and rolling method are: less energy consumption, generally saving about 40%, small equipment investment, short production cycle, conducive to waste recycling, less transportation costs, so that the production cost is much lower. The disadvantage is that the mechanical properties of the products are poor and the quality is not as good as the products produced by traditional methods; Few cast rolling varieties; The output of each unit is small. Continuous casting and rolling products are mainly used in food, construction, automobile and other civil industries. Continuous casting and rolling mostly use industrial pure aluminum and aluminum magnesium alloy with low magnesium content as raw materials. The thickness of strip is generally 6 ~ 10mm, and then the finished strip and foil are produced by cold rolling.